Precision redefined: High-performance linear motors ensure flawless wood panels
- Paxton Shantz
- Apr 1
- 4 min read
Translatory servomotors deliver high-end motion control in repair systems for wood veneers and chipboard

Wood, as a quintessential natural and renewable resource for all kinds of products, usually doesn’t arrive at the factory in perfect condition. To address this, Finnish machine builder Raute—recognized as the global leader in veneer, plywood, and LVL (laminated veneer lumber) production technology—offers advanced repair systems that automatically detect and fix defects. A combination of AL8000 linear motors and AX5000 servo drives from Beckhoff ensures the high precision and dynamics required for the task.
Raute, headquartered in Nastola, Finland, has built up a comprehensive stock of expertise in all sub-processes of veneer, plywood, solid wood panels and LVL processing since the company was founded in 1908. Its technology spectrum ranges from log handling, turning, and drying to veneer handling, stacking and pressing of veneers, panel handling, sorting, and repair. “Today, more than half of the LVL produced worldwide is manufactured on Raute machines,” states Erkki Kauranen, Business Line Manager for Veneer Repair, Panel Repair, and Panel Processing.

Premium solid wood panels with unmatched quality
The Panel Repair Station R5 is Raute’s latest innovation. Automated with PC-based control, the system eliminates the need to manually repair solid wood panels and requires only one operator to monitor the process. This allows companies to deploy their qualified personnel elsewhere in production and, at the same time, increase the quality and efficiency of repairs. When dealing with an average of seven defects per side, the system can repair up to 250 panel surfaces per hour. Designed for processing solid wood panels, the system can also repair panels made from all other types of wood.

All process steps are automated with PC-based control. “We chose the AL8000 linear motors and AX5000 Servo Drive from Beckhoff because of their high precision and dynamics,” says Erkki Kauranen. The system is controlled via TwinCAT and a C6030 ultra-compact Industrial PC. The customer-specific control panel communicates with the Beckhoff Industrial PC via CP-Link 4. Raute uses AM8000 synchronous servomotors with planetary gearboxes for the rotary movements. Given the large system size of 8 x 10 m, sensor signals are collected in a decentralized manner using EtherCAT EP box modules, which feature an IP67 protection rating. TwinSAFE components are used for the safety technology.
A hundred parameters define a knothole
Along with the highly dynamic and fully automated processes, detecting and eliminating defects is crucial to maintaining system productivity and ensuring a steady output of high-quality wood panels. To achieve this, Raute has integrated advanced technologies for identifying and categorizing defects in veneers and plywood panels into specialized systems called analyzers, which rely on image processing and AI. Raute has trained the technology to recognize the patterns and shapes of approximately a thousand different types of knotholes, all categorized as “healthy”.
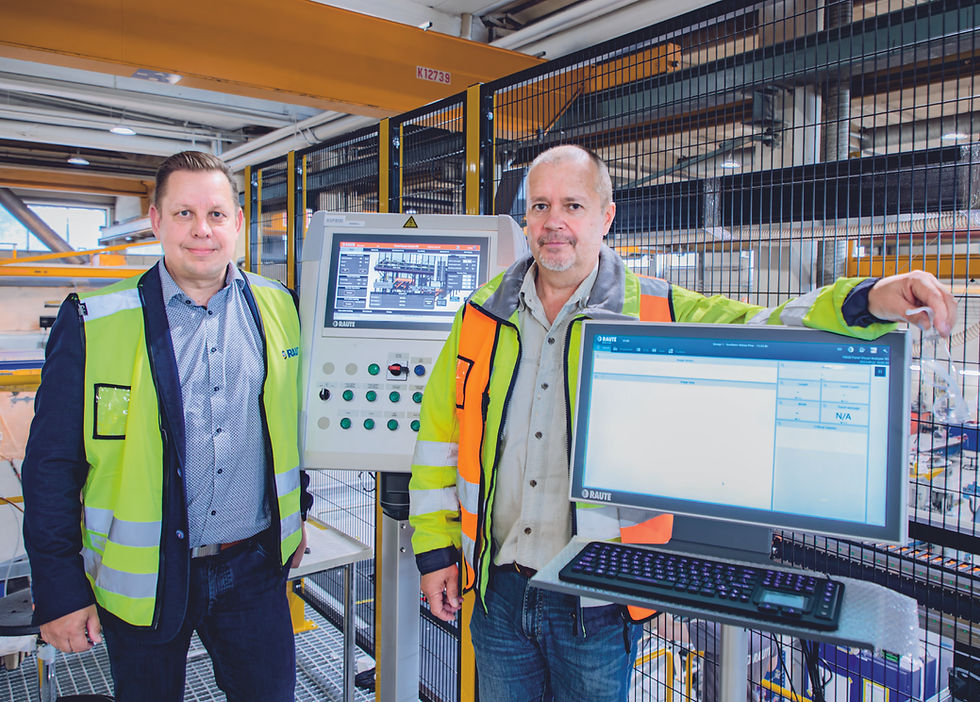
“We detect and document around 100 features in a knothole, such as its shape and color changes,” says Erkki Kauranen, explaining the work involved. This means that powerful hardware is required to record the grain and detect the defects in order to keep the repair system performing well. “That’s why we carry out camera- and AI-based detection and evaluation of the defects on another Beckhoff control cabinet Industrial PC – a C6650,” adds Janne Suhonen, Key Account Manager at Beckhoff Finland.
Typically, between five and 20 defects are detected per panel. Smaller defects may remain untreated, depending on the desired quality level, the product in question, and the intended use. This advanced analysis of the wood panels allows the company to use exactly the right amount of materials for repairs. “We’ve managed to halve our consumption and reduce waste to a minimum,” says Erkki Kauranen. This is demonstrated by a comprehensive reporting system, which plays a key role in the repair systems.
The power of dynamic motion control, unleashed
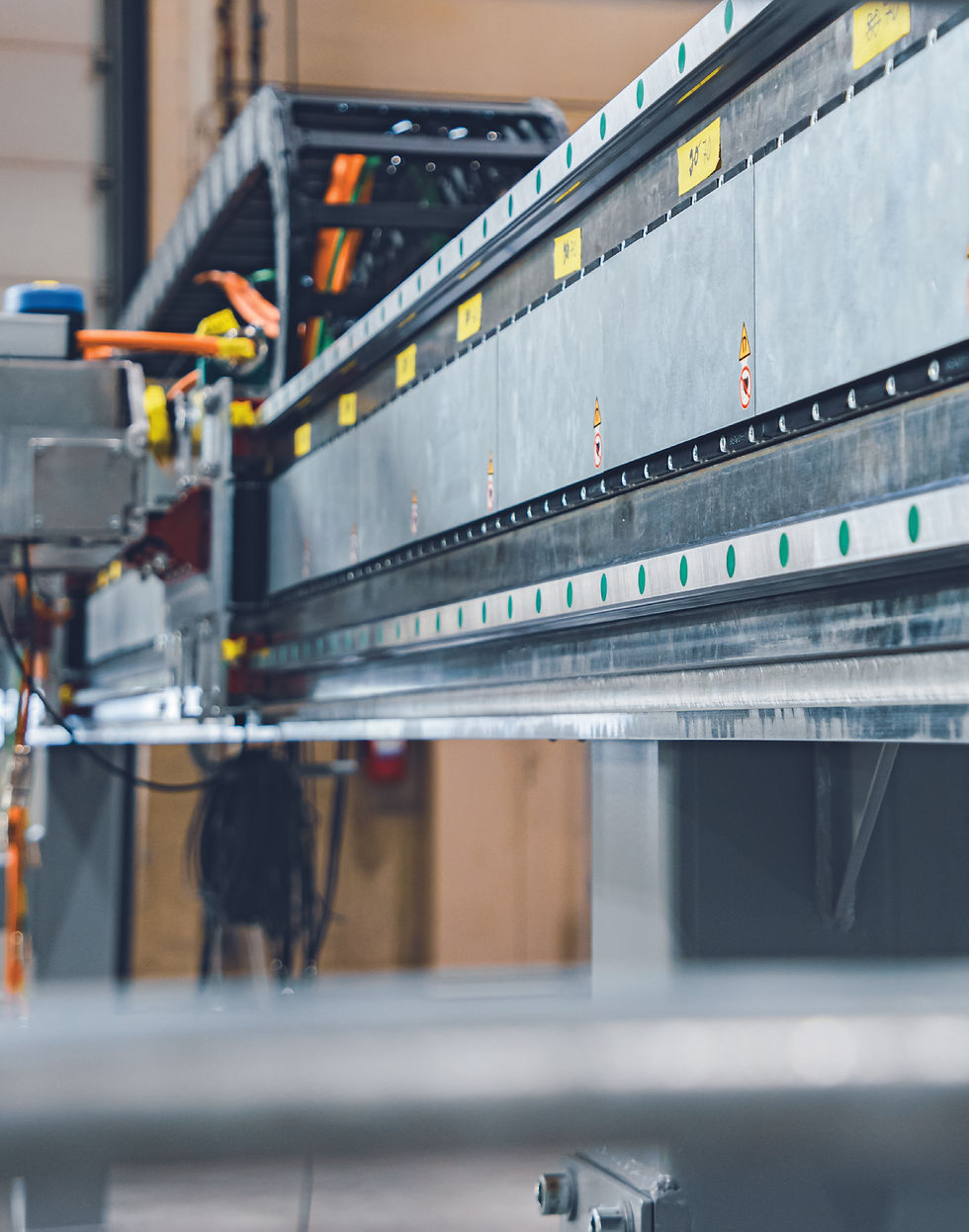
To ensure excellent performance, the repair station relies on advanced automation technology. The coordinates of each defect must be linked to the corresponding wood panel and transferred to the control system. The AL8000 linear motors handle the dynamic and precise positioning of the tools. To maintain high system throughput, multiple tools work on a single veneer simultaneously. However, there is also integrated collision detection to prevent damage to the tools. “The complete solution from Beckhoff, consisting of an engineering environment, control, safety, high-performance motion control and highly dynamic linear motors, has brought us clear advantages in the field – especially during commissioning,” says Erkki Kauranen.
PC-based control has also solved the interface problems that repeatedly arose in the past.
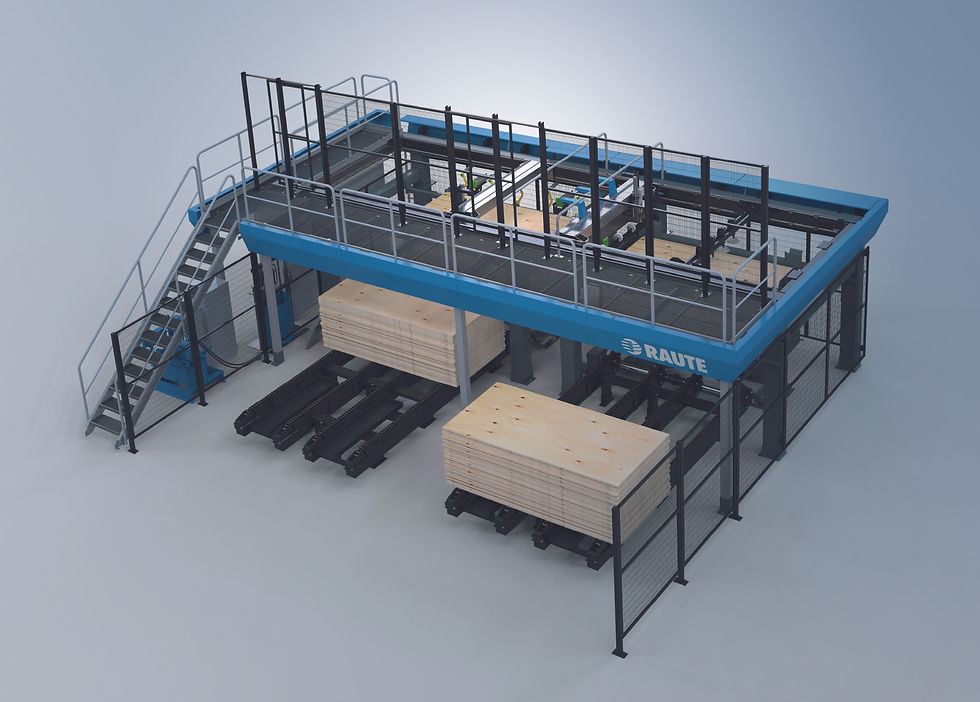
The company began working with Beckhoff about 10 years ago, when it acquired its first drives for lathes and a few I/O terminals, which it used for tasks such as acquiring signals from SSI encoders. Over time, they began using advanced motion controllers and industrial PCs. Teppo Lepistö, Automation Product Specialist at Beckhoff Finland, supported the implementation of the PC-based solution from the very beginning. “That has been a very important factor in introducing new products and control systems, and has accelerated development considerably,” says Erkki Kauranen.
Today, Raute uses Beckhoff’s complete automation portfolio – motors (rotary and linear), drives, and control elements – for its repair systems. The outdated control system for the lathe is currently being replaced by a powerful control system from Beckhoff. The Panel Repair Station R5 has been in operation for some time now and has become a standard-bearer for technology at Raute, providing the basis for future developments.
Ready to ramp up reliability and quality assurance in your own manufacturing and production with next-level automation? Contact your local Beckhoff sales engineer today.

Paxton Shantz is the Digital Manufacturing Industry Manager at Beckhoff Automation LLC
Comments