Motion Control Advances Move Packaging Machines Toward Industry 4.0
- Matt Prellwitz
- Apr 1, 2021
- 6 min read
Updated: Jun 26, 2023
To enable lot-size-1 production, optimize changeovers, footprint and precision in packaging machines with leading-edge servo drive and software solutions

Industry 4.0. The Industrial Internet of Things (IIoT). Lot size 1. It is difficult to talk about automation today, particularly in the packaging industry, without someone throwing around these terms. In practical terms, packaging machine builders and CPG manufacturers continue to look for new ways to enable greater customization while increasing throughput. However, many of these conversations often turn into a laundry list of buzzwords and “what ifs.” And ultimately, the discussions typically do not go beyond connectivity concerns.
While these are important, a regularly overlooked yet critical aspect of Industry 4.0 is drive technology. After all, production, packaging, palletizing and so on all depend on a great deal of motion control in the real world. New motion technologies enable faster changeovers, smaller machine footprints, high-precision torque control for capping and smoother continuous motion. Combined with greater communication and data acquisition capabilities, rotary motors, linear motors and drives complete the overall infrastructure needed to make Industry 4.0 concepts a reality.
Dynamic motion control and faster changeovers
Local mass production down to lot size 1, a key concept in Industry 4.0, is only possible through optimized product flows and rapid changeovers. Achieving this requires extremely dynamic and precise motion, because the costs compound when you have to make a highly individualized product more than once due to mistakes. While linear transport systems are providing greater freedom in machine design, machines often require small, low-cost augmentations rather than a mechatronic redesign. In these cases, new linear motion solutions provide an optimal answer for transporting product from point A to point B, such as in pick and place applications, transfer stations and other movements with high payloads.
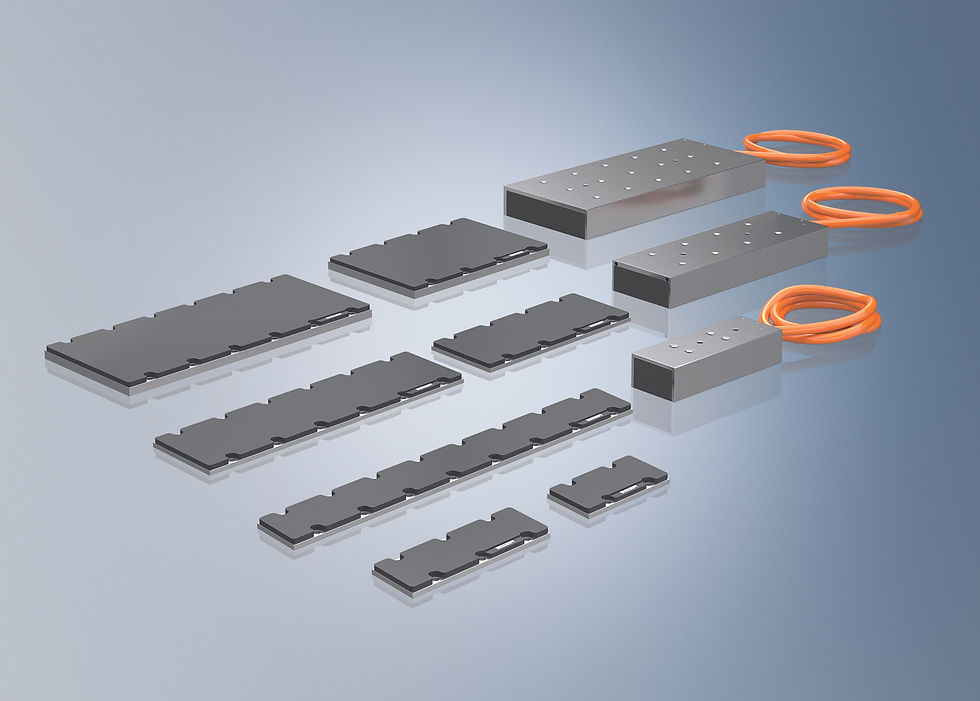
The new AL8000 linear motor series from Beckhoff, for example, uses One Cable Technology (OCT) for the motor and thermal feedback, which reduces the cost of implementing linear motion. A modular concept with consistent design across various sizes simplifies commissioning, while providing more consistent forces and higher performance.
Another option is a direct-drive ball screw, such as the AA3300 linear actuator. This electric cylinder extends up to 200 mm at 10 m/s2 with peak force of roughly 12,500 N. This new solution is ideal for pressing, perforation, sealing and assembly steps in packaging. The AA3300 features OCT, a 24-bit encoder with safety communication, an optional brake and other functionalities, and it is designed in a standard form factor to pair with Beckhoff servo drives.
Even with increased linear motion capabilities, any format changes still pose challenges in traditional machine setups and create unnecessary downtime. Increasing consumer demand for customization and personalization now requires packaging operations to make frequent format changes, e.g. switch from 9- to 18-ounce cereal boxes, from six cookies in a package to a dozen or from a standard wrapper to a seasonal one. Adapting a machine too often requires an operator to manually adjust the machine with a hand crank connected to a ball screw. Engineers can solve this by installing a compact servomotor in place of the hand crank to move the ball screw. However, they could also use a more direct solution like the AA3300 linear actuator to move tooling one way and the other. These options enable immediate, software-based changeovers, rather than time-consuming manual processes.
Decrease packaging machine footprint
While uptime is money in packaging, so is floor space. Automation vendors have begun shrinking servomotor and servo drive footprint by implementing compact motion drive options and even integrating both technologies in a single device. New ultra-compact drive technologies place high-performance servo components directly into a standard I/O segment on DIN rail.

The ELM72xx series from Beckhoff, for example, delivers 4.5 to 16 A, one- and two-channel options and OCT to minimize cabling requirements. Most technologies become more powerful and cost effective as they advance, and this area is no exception: The ELM72xx series reduces costs by about 40% compared to current designs, while adding new features. By using the same controller board as larger servo drives, it offers integrated Safe Torque Off (STO) and Safe Stop 1 (SS1) or a comprehensive Safe Motion package, along with faster scan times and higher filters. While compact motion will not replace standard drive components in all cases, it will meet the needs in many situations, significantly reducing control cabinet sizes as a result.
Moving outside of the control cabinet entirely, distributed servo concepts allow engineers to free up critical space on the factory floor. Now in addition to incorporating the drive electronics in one IP65 device, engineers can integrate another system directly into the motor: EtherCAT I/O. By enabling communication to peripheral field devices, integrated servo systems, such as the AMI821x series from Beckhoff, deliver standstill torques from 0.5 to 1.1 Nm, optional STO functionality and multi-turn absolute encoder. An M12 interface supplies power for the motor and electronics, while two M8 connectors allows for easy connection of EtherCAT to sensors or actuators, reducing component count and cabinet requirements.
Advanced software powers high-precision motion control
Beyond advances in hardware, new functionality in automation software allows packaging operations to increase throughput and quality. A fully integrated automation architecture makes it easier to bridge the gap from the cloud to the controls level. As such, TwinCAT 3 automation software and the wide-ranging libraries built into it provide the necessary toolkit to increase precision and make smoother movements in motion control. Beyond standard motion control functions in TwinCAT, torque control and anti-cogging are both examples of practical features that can help make Industry 4.0 concepts possible at the machine level.
Torque control enables faster capping for all types of products, for instance. Traditionally, engineers had to limit the velocity on motion axes to avoid over-tightening. This new functionality is important in capping if, for some reason, the bottle is damaged before arriving at the capping station or if the material is susceptible to breaking due to the torque required to tighten the cap. All Beckhoff drives offer the MC Torque Control functionality built into TwinCAT, which can control the torque as well as the velocity to get to that torque. That is, it makes sure the cap is properly tightened as fast as possible with minimal risk of damage.

With torque control functionality, engineers could also program the axes to hold the torque for a set period – let’s say 1 second. If it is not able to maintain the set torque for that 1 second, the system can tell if the bottle is damaged or otherwise defective, and then reject it. Not only does this increase throughput, but it also allows for greater customization with multiple motion profiles for bottles of different sizes, materials and so on when combined with the necessary technologies for fast changeovers.
For smoother motion, servo axes can now use software-based anti-cogging. This functionality for drive control compensates for the spacing of magnets in the servomotor to ensure precise movement at any point. Anti-cogging benefits many packaging applications, such as winders, flow wrappers, vertical form/fill/seal machines or any machine that needs to pull product or packaging at a constant velocity with the absolute minimum ripple. Surfacing applications also require this when placing a label on a product or achieving a smoother print on the package. Anti-cogging can be implemented in any Beckhoff servo drive, including the compact motion options up to larger format AX5000 and AX8000 servo systems. This means it can control motors from standard IP65 options to IP69K anodized aluminum and stainless steel options for wash-down applications.
All industrial technologies contribute to Industry 4.0
In the end, digitization must be more than digital to truly matter in manufacturing. Of course, it is important to collect the relevant performance and quality assurance data, transfer data to the cloud and perform processing with advanced algorithms. All of this allows engineers to further enhance the performance of packaging machines. A fully integrated automation ecosystem for control, fieldbus and motion control makes it easier to sample data on a microsecond level and implement a non-real-time interface to that library. In fact, these technologies are foundational to Industry 4.0 and necessary to make cloud-based systems worthwhile. Turning the concepts into reality, however, requires advanced motion control software and hardware to make and move things in the real world.
Are you ready to boost machine performance in packaging with Industry 4.0-ready motion technologies? Contact your local Beckhoff sales engineer today.

Matt Prellwitz is the Drive Technology Product Manager for Beckhoff Automation LLC.
A version of this article previously appeared in Packaging Strategies.
Comments