Sustainability in Additive Manufacturing Goes Full Circle
- Paxton Shantz
- Nov 16, 2023
- 5 min read
Updated: Dec 28, 2023
Ponticon harnesses robotics and fast, flexible automation technologies from Beckhoff, including TwinCAT CNC, to explore circular economy concepts

Lasers! Robots! Additive manufacturing! Does this get your attention? The latest digital manufacturing solutions from Ponticon GmbH check many boxes in terms of the latest industry trends. But the impressive technology goes beyond the buzz to empower new production and component repair capabilities for regenerative economy concepts.
With its pE3D system, the Wiesbaden, Germany-company enables more efficient additive manufacturing of complex, symmetrical geometries. With the system, components up to 700 millimeters in diameter and 800 millimeters in height can be coated, completely rebuilt or repaired with material thicknesses of 50-200 micrometers.

The pE3D system from Ponticon is a real industry leader, yes, not only in terms of application technology but also construction technology. Constructed from solid granite slabs up to 20 centimeters thick, the base frame stands over 3 meters tall and weighs over 7 metric tons.
“If you want to build up large components in a highly dynamic and precise process or apply an ultra-thin coating, you need a rigid structure,” says Thomas Horr, Managing Director of Ponticon.
The 3DMD (Dynamic Material Deposition) process developed by Ponticon uses laser cladding to manufacture complex component geometries from virtually any combination of materials. For this purpose, high feed rates with the smallest possible deviations are vital. With a path accuracy of a few hundredths of a millimeter, the pE3D system not only works with precision but also offers extraordinary dynamics, with feed rates of up to 200 m/min and acceleration of up to 5g, according to Horr.
Putting the repair capabilities to the test, Ponticon recently delivered a machine cell including the pE3D system to help researchers explore new ways to reduce waste in manufacturing. The machine at the wbk Institute of Production Science at the Karlsruhe Institute of Technology (KIT) in Karlsruhe, Germany, was funded by the EU and the Ministry of Science, Research and Arts Baden-Württemberg. The aim of the InRePro project is to investigate the circular production of components on an industrial scale.
Additive manufacturing system melds flexibility and speed
The pE3D system’s high feed rate results from the special design: a parallel kinematic system. Typically, parallel kinematics are very fast but not precise. By using special mechanical elements, Ponticon has eliminated this shortcoming in its tripod. The rotary/swivel unit acts as fourth and fifth axes. This provides additional flexibility for machining complex geometries. The engineering team met the requirements for precise control and coordination of the tripod, rotary/swivel table, and laser with PC-based automation from Beckhoff.

For machining in the standard operating mode, the component is clamped on the tripod and moved under the laser unit, which is in a fixed position. In the second configuration as a 5-axis CNC, however, the complete laser head is mounted on the tripod. “To do this, we simply use the frame, which was previously used as a workpiece carrier,” Horr says.
The component is then clamped on the rotary/swivel unit below and can also rotate and tilt. This allows powdered metals and alloys to be deposited on surfaces of any shape. The table comes into play when the geometry of the workpiece requires reorientation to achieve overhangs or certain angles, or to build up rotationally symmetrical parts while maintaining the feed rate.
These key features place major demands on the mechanical structure. In addition, the control system must be able to keep up with the dynamics of the system, particularly when controlling peripheral devices. “The most important thing is to ensure that the switching times of the laser are precise,” adds Horr, “so that the laser switches at the right position and melts the material correctly.”
XFC and TwinCAT CNC speed up production
For rapid response rates, Ponticon relies on eXtreme Fast Control (XFC) solutions from Beckhoff in conjunction with EL2262 oversampling terminals. XFC is based on an optimized control and communication architecture for high-end automation applications. This uses the combination of an advanced Industrial PC (IPC), ultra-fast I/O terminals with extended real-time characteristics, the real-time EtherCAT industrial Ethernet system and TwinCAT 3 automation software. XFC makes it possible to achieve I/O response times of less than 100 microseconds.
Dynamic tripod movements require the pE3D to specify the axis setpoints at high frequency. The actual values must be returned just as fast. EtherCAT offers the performance needed for this. In addition, Safety over EtherCAT (FSoE) supports integrated, programmable safety over the same network.
Path control of the tripod and rotary/swivel table is implemented via TwinCAT CNC. For this purpose, the axis controllers are configured for maximum dynamics and operate with minimal lag, explains Horr: “A lot of development work has gone into the corresponding function blocks that we use for control optimization.”
The kinematic transformation for the tripod built into TwinCAT, not to mention the flexibility of PC-based control, made Beckhoff an obvious solution for Ponticon. Using TwinCAT CNC, the developers only needed to configure the kinematics and had no additional development work.
“Particularly in the initial phase, when it is not possible to formulate the task so clearly, what is needed is flexibility. TwinCAT and the software licensing model from Beckhoff offer that,” Horr says. “We were surprised at how quickly we were able to get everything up and running. And if there were any hurdles to overcome, support was available quickly, such as when there were questions about the implementation of the oversampling terminals. The collaboration with the experts from Beckhoff has been exactly what we had hoped for when choosing our automation system partner.”
Additive manufacturing for more sustainable production
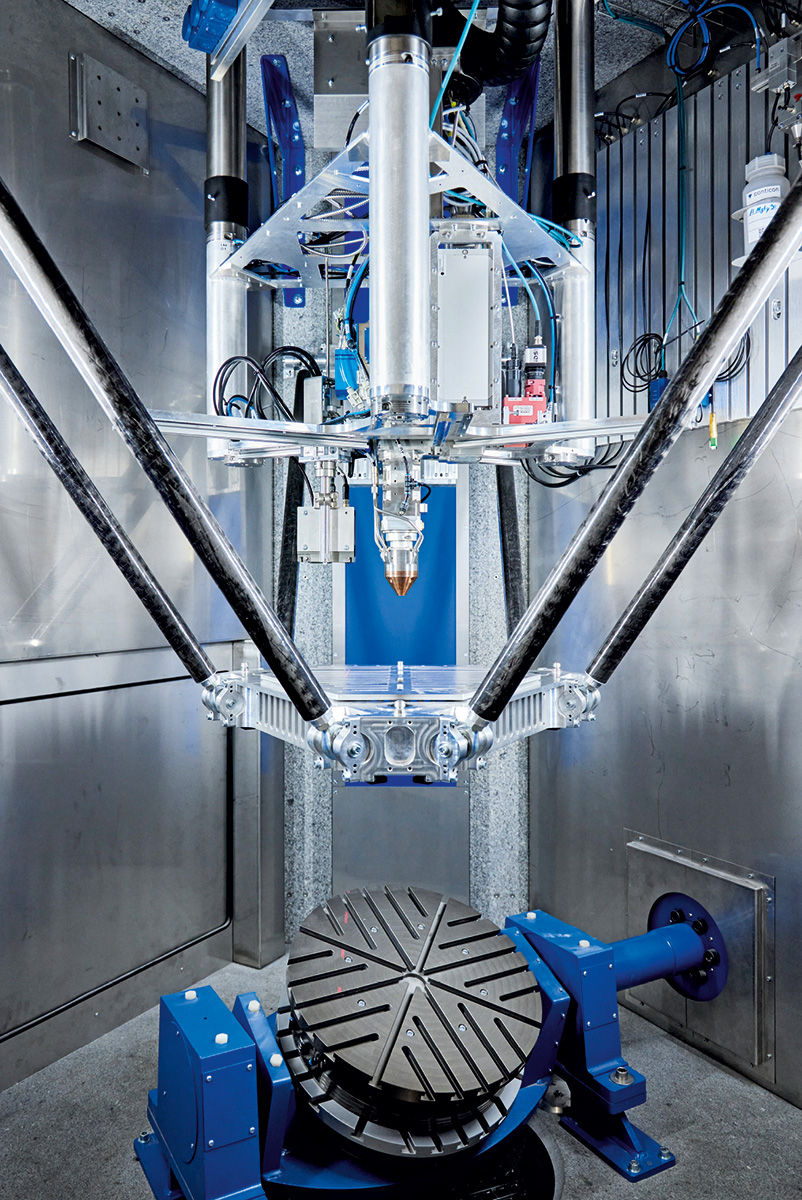
The Ponticon system has become an essential component of the InRePro research project, according to Prof. Frederik Zanger, Director of KIT’s wbk Institute of Production Science. InRePro is short for “Inspection and remanufacturing cell with process-integrated multi-sensor technology for a digital-autonomous manufacturing process.” Refurbishing subsystems and components can reduce consumption of raw materials and energy. In turn, this enables sustainable, circular economy concepts using automated, large-scale production.
Combining the 5-axis laser cladding system with a 5-axis machining center enables flexible reconditioning of components. The multi-sensor process monitoring solution integrated into the pE3D system provides immediate information about manufacturing quality during the machining process. Corresponding sensors (OCT, quotient pyrometer, WeldWatcher) are integrated into the laser head, which enable melting zone monitoring. A tracked 3D laser scanner measures the material deposition results over a geometric area immediately after the process. So the system can systematically observe and investigate the causes of defects in the process.
“The project began during a period of economic uncertainty. Nobody knew what would happen to the delivery times for the various components,” Zanger says. “Today, we are delighted that everything has run smoothly in our collaboration with Ponticon.”
Following the success at wbk, Ponticon continues to explore new ways to leverage the flexibility of PC-based control in future projects. After all, additive manufacturing isn’t tied to any particular kinematics, and the company’s existing developments are easy to apply to new applications using TwinCAT, explains Horr: “We are confident that we will be able to port the previous developments on the Beckhoff platform to other kinematics, such as a 6-axis robot.”
Want to boost performance of your digital manufacturing equipment with scalable, secure PC-based automation? Contact your local Beckhoff sales engineer today.

Paxton Shantz is the Digital Manufacturing Industry Manager at Beckhoff Automation LLC
Comments