CMD Converting Machine Delivers the Goods for E-comm Packaging
- Madeline Donkers-Lundquist
- Oct 22, 2024
- 9 min read
Updated: May 14
The 1400-GEC system achieves throughput of 200-feet-per-minute with unmatched speed and efficiency using breakthrough automation technologies from Beckhoff
When an online order reaches your doorstep, it’s imperative that the packaging holds up during shipping. To ensure your parcel arrives safely and in perfect condition, CMD Corp. implements next-level automation technologies at its headquarters in Appleton, Wisconsin. CMD understands that flexible automation and repeatable results are essential in the packaging industry. So the OEM strives to meet customer needs by designing and building highly customized converting solutions.
As a mainstay in the industry, CMD has manufactured high-speed converting and packaging machines for over 40 years. CMD is the global leader of drawtape bag making technology. With a commitment to “making it better together,” CMD focuses on high-performance solutions for clients in the packaging, converting, automation and renewable energy industries. They also constantly explore new technologies that fuel their innovation, as highlighted by the numerous patents showcased in the CMD Technology Center. Through continuous transformation, CMD lives up to its name, which is an acronym for Custom Machinery Design.

The CMD engineering and product teams started designing the new 1400-GEC mailer packaging machine more than a year ago. A high throughput machine with an intuitive operator interface was a top priority, according to Scott Fuller, Product Line Manager, Intermittent Motion Products at CMD. “This new machine is much faster and more automated, which was key for our end user customer,” says Fuller.
The machine manufactures plastic mailer packaging in a streamlined process, converting film from two rolls, registering the print on those two rolls and slitting in up to five individual lanes of bags. The bags are then packed into boxes using an automated casing management system. PC-based automation from Beckhoff, including high precision servo drives and state-of-the-art HMI design software, power this custom converting solution.
Thinking outside the bag for machine building
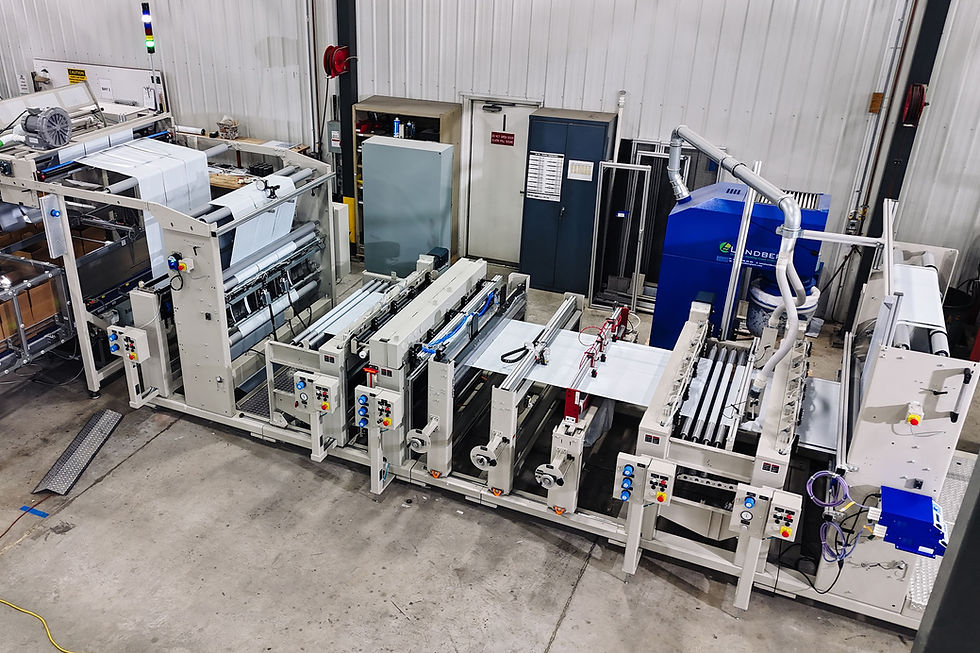
By introducing a new machine design, this project proved to be a significant feat for the CMD engineering and product teams. CMD’s converting customer will produce bags for online retailers primarily to ship e-commerce items in plastic bags. The initial concept for this project was driven by specific customer needs, particularly to create bags that would work with automated product loading.
“A client approached us as they were seeking to improve throughput in their existing machinery. That went for both their aging equipment and their newer machines that weren’t offering the performance they needed. The customer challenged us to boost their throughput and design a production line that performs up to their standards,” says Fuller.
To address all application requirements, the 1400-GEC unspools two rolls of film, registers the print on those two rolls and applies a continuous longitudinal seal. Then it runs the stacked master rolls of film through a series of cross-directional punches and seals, slits the material into multiple rows of bags, and adds perforation for easy separation. Before loading the finished bags into cases, as specified by the customer, the system performs a vision test while blowing air into the open end of the bag and measuring its shape profile.

“This machine incorporates entirely new automation processes. It transitions from continuous motion to intermittent motion and back to continuous in the outfeed, while handling various tasks in each phase,” Fuller explains. “That makes it distinct from the machines we've designed before.”
All this functionality required significant processing power and real-time communication. In addition, the CMD engineering and product teams faced tight lead times on this project. It was essential to finish on schedule while also ensuring the smoothest, most successful outcome.
CMD found robust, cost-effective and user-friendly automation solutions with PC-based control from Beckhoff. Local application and sales engineers from Beckhoff USA helped support the project’s success. In addition, dedicated resources from Beckhoff’s Special Project Team helped boost standard support and systems integration services even further by providing in-depth technical expertise in TwinCAT 3 automation software, motion control and industrial networking with EtherCAT.
“It was important to get the Beckhoff team on board early in both the planning and development phases to help us meet the time requirements,” Fuller says. “It was a benefit to have the Beckhoff team help us lay out the controls architecture and the overall structure of what we wanted to do with the machine.”
Unboxing a new level of efficiency with powerful programming tools
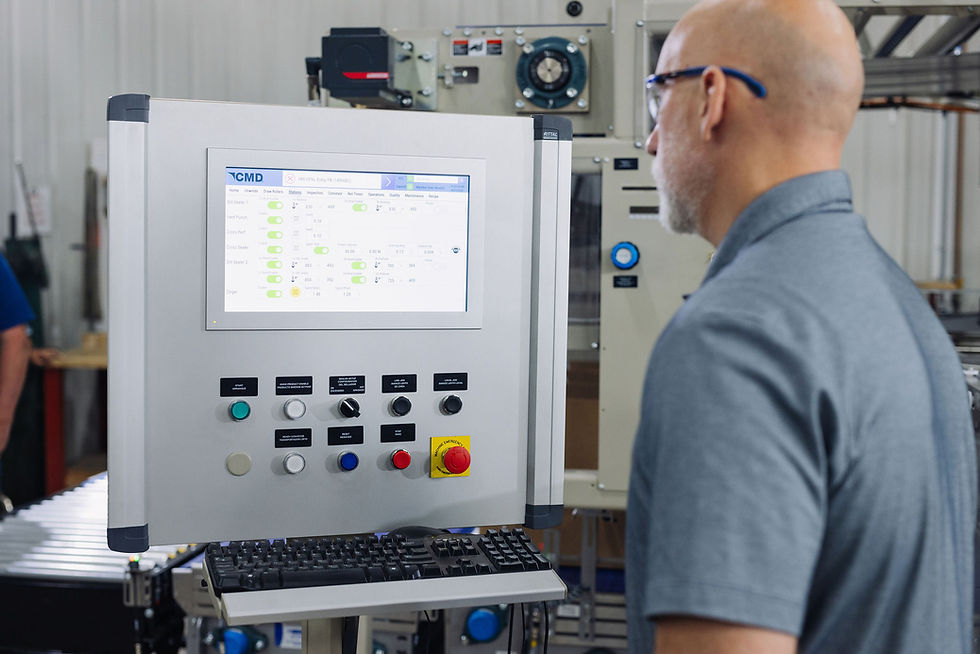
CMD collaborated closely with the Special Projects team to program the machine control in TwinCAT. This end-to-end engineering and runtime platform combines everything from PLC and motion control to integrated safety and IoT. A core package for the CMD team was TwinCAT HMI, which allowed CMD to leverage modern web design standards, such as HTML5, JavaScript and CSS, in industrial applications. This transition streamlined CMD’s programming processes while enhancing the user interface, according to Software Engineer Adam Benson.
In general, the CMD team emphasized ease of use and code reusability while designing their new mailer packaging machine. With the SPT Framework – short for Special Projects Team – the CMD engineers found the perfect tool to standardize their code. This will help CMD maximize its engineering capacity moving forward, according to Don Seichter, area sales manager with Beckhoff USA.
“Given CMD’s numerous equipment customizations, the SPT Framework is an ideal choice. It allows them to create equipment modules for a specific system, reuse those modules in the next customized design, and adapt with new modules for the custom pieces of the equipment,” explains Seichter.
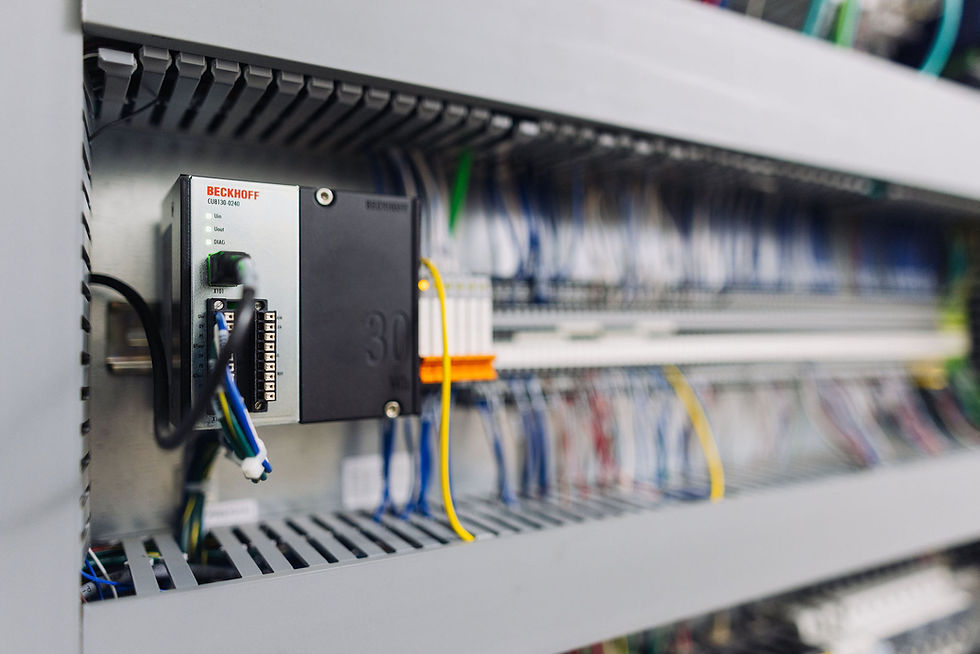
The SPT Framework builds on the ISA-TR88 or PackML standard and the associated libraries in TwinCAT, with some options already accounted for so programmers don’t have to start from scratch. This empowers engineering teams to reuse existing code for future applications while easily customizing it to the requirements at hand.
“Our team started working on the SPT Framework in 2018 after watching how long it took engineers to essentially reinvent the wheel by having to write code for the most basic programming aspects. Then we released the current, tested version on GitHub for anyone to use for free in 2022,” says Mark Lewis, Special Projects Team Manager at Beckhoff USA.
The Special Projects team guided CMD in smoothly transitioning to the PackML standard, enabling them to organize programming into different packages. The standard approach to creating code makes it easier for new engineers to work on a project or troubleshoot machinery without decoding what other, often unknown engineers were thinking when they created it.
“Engineers aren’t interchangeable commodities or drop-in replacements. You can’t grab a few off the street, throw them at a problem, and expect they’ll be instantly effective,” Lewis adds. “That’s really the biggest benefit of leveraging the SPT Framework: It shortens your engineers’ time to effectiveness. That was a huge advantage with this project at CMD.”
Packing all automation technologies into one toolbox

To provide the necessary processing power, the 1400-GEC machine uses a CX2033 Embedded PC from Beckhoff. The DIN rail mounted CX2033 serves as the sole machine controller for the 1400-GEC mailer packaging machine. A dual-core AMD Ryzen™ processor supplies extensive performance capabilities with room to grow. This helped execute the machine control logic and operator interface efficiently – all on one device.
“If you're working with a resource-constrained system, your HMI will be very laggy to the touch. So, putting the HMI server on a CX2033, which offers ample computing resources, enables the touch panel to operate very responsively,” explains Benson.
Modularity, flexibility and high synchronization were essential for the plastic mailer machine. The EtherCAT industrial Ethernet system and EtherCAT I/O Terminals from Beckhoff boosted these capabilities. For example, EK1914 EtherCAT couplers integrate EtherCAT communication with standard and safe I/O terminals to create a space-saving design. The EK1914 offers a mix of standard digital inputs and outputs with several designated for integrated TwinSAFE functionality. This allows CMD to allocate a small amount of functional safety, such as an e-stop, on each tool in the machine line.
“We implemented a fully modern design for this machine, with many stations that accommodate all possible components. The EK1914 adapter provides a compact and cost-effective solution for distributing the I/O and safety hardware closer to the tools,” explains CMD Electrical Engineer Jason Plutz.
The high level of synchronization provided by EtherCAT also enhanced CMD’s motion-intensive application. The CMD team generated additional performance increases with drive technology from Beckhoff. The 1400-GEC mailer packaging machine features AX8000 multi-axis servo system and AM8000 servomotors controlling fourteen axes. The space-saving design of Beckhoff’s drive technology – such as gap-free drive module installation and One Cable Technology (OCT) – were a major attraction for CMD.

“The AX8000 drives are very compact for the power they provide,” Plutz says. “And by using the integrated Safe Torque Off (STO) functionality, we eliminated two large contactors, saving significant panel space.”
The proven EtherCAT-based AX8000 drives offer robust functionality and energy efficiency. EtherCAT offers ultra-fast cycle times below 100 µs and simplifies the selection and installation of all kinds of industrial devices that are available from Beckhoff and a vast range of other vendors in the EtherCAT Technology Group.
To enable unique motion profiles, CMD leveraged camming motion control in TwinCAT 3 software with two of the axes on the bag packaging machine. The bag opener, initially positioned in the intermittent movement section, was relocated downstream to enhance efficiency through the camming functionality. Using a continuous web, the bag opener is precisely cammed to achieve the desired motion at just the right moment.
Controls consistency and efficiency are a package deal
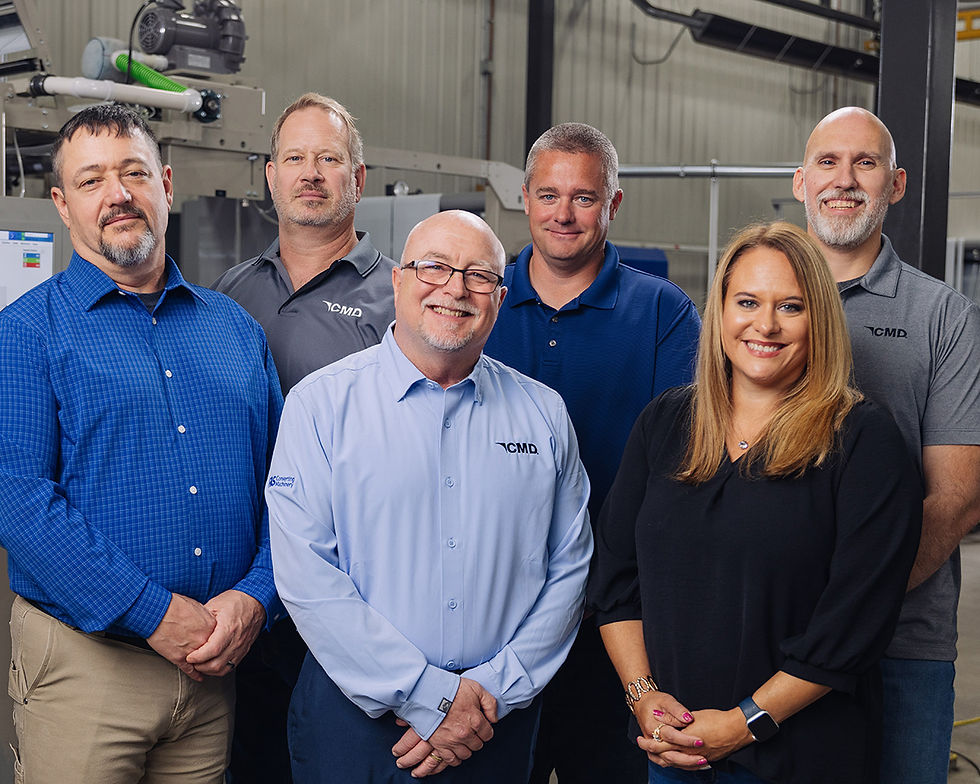
Harnessing New Automation Technology from Beckhoff in the 1400-GEC application enhanced CMD’s engineering capabilities going forward. By harnessing the SPT Framework, the CMD engineering team boosted their code reusability to 90%. Employing TwinCAT HMI also helped the team create a more intuitive operator interface in a way that supports outstanding customization and reuse. “The new operator interface resembles our legacy HMI, but has a much cleaner, more user-friendly design,” says Benson.

Running the entire machine with an EtherCAT-networked CX2033 Embedded PC accelerated CMD’s scan times to 2 milliseconds.
“Having everything scan at one high speed is a huge benefit. You don't have to worry about communicating between process stations that function at different speeds because everything updates at the same time,” Plutz explains.
This enabled the CMD team to reach their target throughput rate of 200 feet of plastic sheet per minute. This translates to 100 bags per minute per lane, resulting in an impressive total of 300 to 500 bags produced every minute. The associated EtherCAT I/O and TwinSAFE I/O terminals also minimized the machine footprint while enhancing network configuration.
Looking ahead, the CMD team intends to scale up to the CX2043 with a quad-core AMD Ryzen™ V1807B CPU for even greater machine control horsepower. Beckhoff's nearly endless IPC portfolio is built for scalability, enabling performance adjustments and controller migration without requiring reengineering. Ongoing support from the local Beckhoff team will remain vital, just as it was during the design and implementation of the 1400-GEC plastic mailer machine.
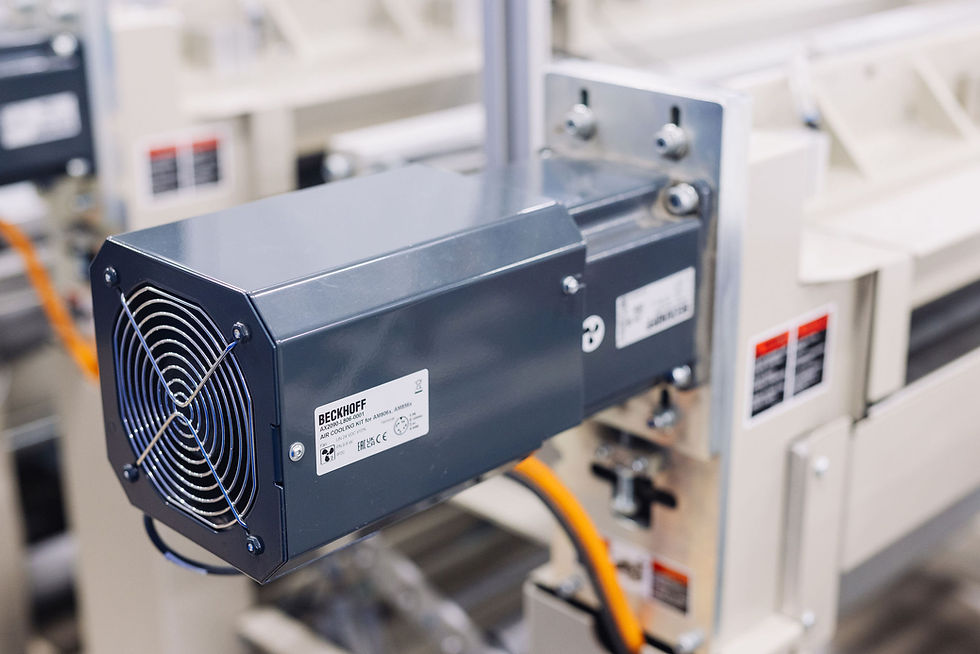
“We received incredible support from Beckhoff, and I don't think we would be where we are without all of that support,” says Plutz.
The collaboration between the CMD team and Beckhoff’s local engineering and sales teams were essential to the successful completion of this project. “Beckhoff provided significant added value by helping us get up to speed on this project, but also provided the framework to allow us to more rapidly deploy future development projects,” Fuller says. “That support was central to our success on this project and will play a crucial role in our future success.”
Ready to ship an entirely new solution and enhanced for e-comm packaging? Reach out to your local Beckhoff sales engineer today.
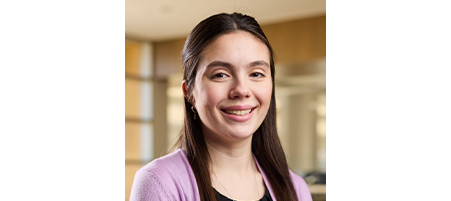
Madeline Donkers-Lundquist is the Social Media & Content Specialist at Beckhoff Automation LLC.
Comments