5 Automation Advances That Reinvigorate Innovation in Packaging
- Mark Ruberg
- Jul 7, 2021
- 5 min read
Updated: Jun 26, 2023
A year of difficulty and change proved that there’s no time like the present to modernize packaging machines with connected and adaptive automation technologies

It’s time to reinvigorate innovation in packaging. The pandemic affected nearly every part of our lives, and it certainly left a mark on the packaging industry. In many areas, SKU proliferation slowed as CPG manufacturers searched for ways to produce enough food and other goods with fewer staff on a line or in a plant at the same time. Manual changeovers became a health and safety concern. Customization took a backseat to quota because the technology wasn’t in place to deliver both.
Remote maintenance and troubleshooting were no longer a nice bonus for machines. Similarly, the virtual FAT became standard for the same reason. Companies predictably saved time and money by not sending engineers across the country. They also found remote troubleshooting solved issues quickly, and virtual FATs didn’t create a spike in performance issues. The automation technologies worked how they should, and manufacturers that standardized on flexible controls, motion and networking technologies adapted faster and with fewer pain points.
However, most of these technologies had been within reach for a long time, and the advantages had simply been waiting. As one engineer at a large OEM customer recently put it: “Necessity is not necessarily the mother of invention, but the mother of innovation.” Now that the packaging industry is moving forward, it’s time to begin implementing leading-edge automation technologies that create new possibilities, deliver greater efficiencies and help you prepare for future disruptions. It’s time to turn those Industrie 4.0 and IIoT concepts into real-world applications.
Here are five automation advances to consider for your R&D projects and new machine designs.
1. Mechatronics for unlimited flexibility and customization

Mechatronic systems provide revolutionary new capabilities to packaging operations. The linear eXtended Transport System (XTS) from Beckhoff enables instant changeovers, greater flexibility and footprint reductions up to 50%. The fully integrated motor modules contain all power electronics, and movers can operate individually or in groups. Engineers are revolutionizing applications to incorporate the new design freedom inherent to XTS. Simple examples include doubling or tripling the throughput of slower processing stations as well as adding tooling or linking movers to carry larger payloads. The XPlanar system elevates these capabilities, using flying motion with freely arrangeable motor tiles and levitating movers to transport product to only the necessary stations, bypassing others. With automatic collision avoidance, path planning, anti-slosh, 360-degree rotation and more, the system enables true lot-size-1 production for packaging, pharma and food processing applications. With XTS and XPlanar, the choice between customization or quota is no longer necessary. Productivity and flexibility are both enhanced.
2. Optimized drive technology to make machines adapt

Maybe your machine is small or low-cost or simply not a perfect fit for new mechatronics. Even so, traditional motion control concepts will no longer cut it if the goal is to make Industrie 4.0 concepts a reality. Beckhoff continues to release motion technologies for faster changeovers, smaller machine footprints and smoother, higher-precision motion. With One Cable Technology (OCT) and support for two motors per module, the ELM72xx series compact drives reduce costs by roughly 40%, add new features and cut footprint through a space-saving I/O form factor. The AMI812x integrated servo system combines a drive and motor into one housing and provides standstill torques from 0.5 to 1.1 Nm, optional STO functionality and multi-turn absolute encoder, while incorporating EtherCAT I/Os for peripheral field devices. These, among other drive technology advances from Beckhoff, bundle greater communication, data acquisition capabilities and smaller footprint to help engineers and maintenance staff continue optimizing machine performance while reducing floor space requirements.
3. Scalable controllers and multi-touch HMI hardware

Delivering the computing power for smart machines requires robust hardware that can support control logic as well as advanced connectivity, inspection, predictive maintenance and onboard machine learning (ML). The best way to accomplish all this is through a single PC-based controller. This eliminates the communication latency that is common between multiple hardware “black boxes” for PLC, motion control, robotics and other functions as found in traditional architectures. Beckhoff offers a scalable portfolio from micro-controllers with ARM CPUs all the way up to industrial servers with 40-core Intel Xeon processors and multiple OS options. Devices in the ultra-compact C60xx Industrial PC series, for example, can support basic to advanced machine control and serve as IIoT gateways at the same time. Beckhoff also offers Panel PCs, which combine HMI and machine control in a single device, and a complete line of Control Panels built to withstand even the toughest packaging environments.
4. Flexible networking and I/O for greater data insights
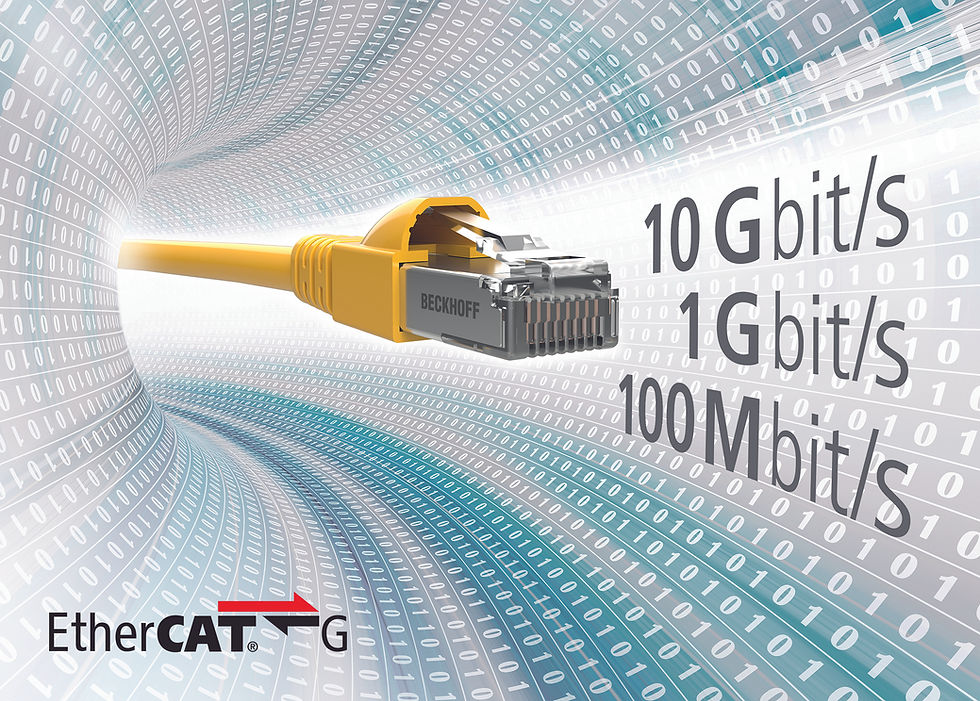
As machines increase in complexity, real-time communication between the controller and field devices is more critical than ever before. The deterministic EtherCAT industrial Ethernet system remains the fastest fieldbus available. EtherCAT G and G10 will increase these speeds to 1 Gbit/s and 10 Gbit/s, respectively, and provide the higher bandwidth required by data-intensive vision, mechatronics and other systems. XPlanar, for example, uses EtherCAT G due to its massive amounts of motion feedback. However, EtherCAT G, as an extension of the base technology, remains fully compatible with existing 100-Mbit/s EtherCAT networks, and the two can mix with the simple addition of a branch controller. Combined with compact IP20 up to IP69K form factors, integrated safety, high-end measurement, couplers to connect with more than 30 prominent fieldbuses and more, Beckhoff I/O solutions are leading the way for open communication on smart packaging machines.
5. Powerful, yet accessible, control, IoT and ML solutions
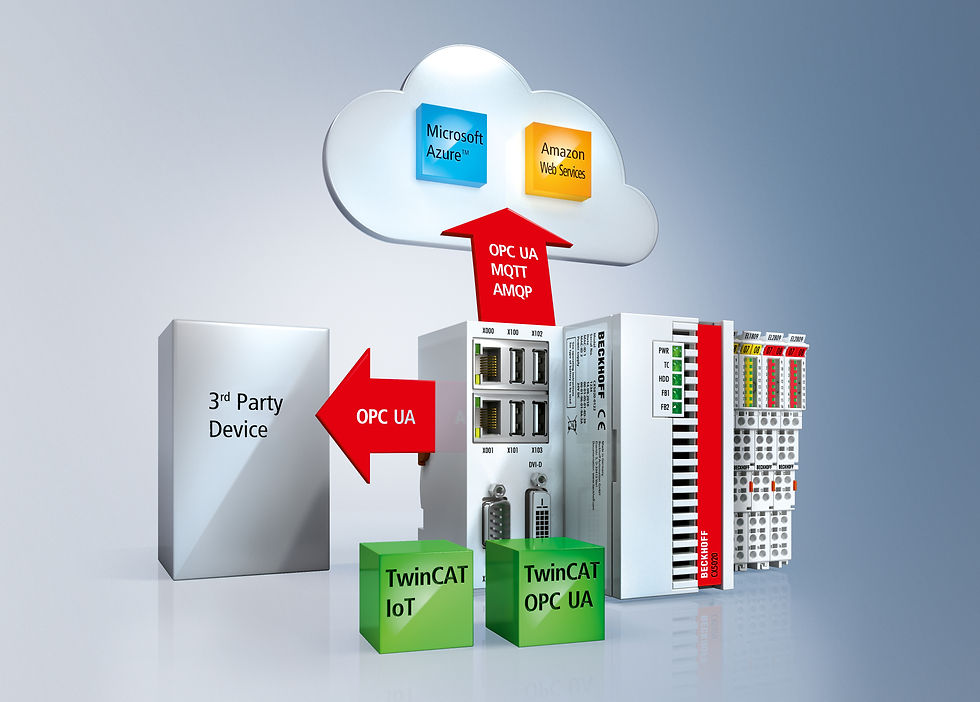
Of course, no Industrie 4.0 or IIoT system can exist without effective software solutions. Here also, a fully integrated approach yields greater results. But adding functionality beyond the standard controls world can often seem daunting and require expensive programming and support from outside experts. TwinCAT 3 automation software, however, offers a comprehensive engineering and runtime environment with programming in standard PLC languages, function blocks and computer science standards. This allows controls engineers to take on projects involving vision, HMI, analytics and even ML applications inside the familiar Microsoft Visual Studio environment, alongside standard motion and control logic. Beckhoff also supports open vertical communication standards, including OPC UA, MQTT and AMQP. As a result, engineering becomes faster and more effective while simplifying remote support and OEE monitoring. The Beckhoff portfolio natively facilitates horizontal and vertical secure communication within today’s standard protocols. And did I mention you can download the TwinCAT engineering software and start programming for free?
Build packaging machines to handle tomorrow’s challenges
Change is hard. And getting buy-in for upgrades and redesigns can be difficult. But as we saw during the pandemic, production didn’t grind to a halt because engineers added new technologies to packaging machines, but it may have if they had decided not to try anything new. Another thing the pandemic taught us is people are resilient, and making packaging machines that work better and more efficiently helps everyone in the end – the initial learning curve becomes a springboard to long-lasting technology advancements.
While there are smaller ways to begin your digital transformation today – e.g., adding a smart sensor and IoT coupler to a legacy machine – a fully integrated, connected approach is the best way to build going forward, making sure your machine has the data needed to show how it should adapt, but also the mechanical and networking flexibility to physically execute the adaptations needed from actionable data.
By reinvigorating packaging machines with these five automation technology areas, you can ensure that your operation will increase capabilities while being more reliable during the next disruption.
Ready to reinvigorate your packaging machine innovation with a comprehensive automation and IoT solution? Contact your local Beckhoff sales engineer today.
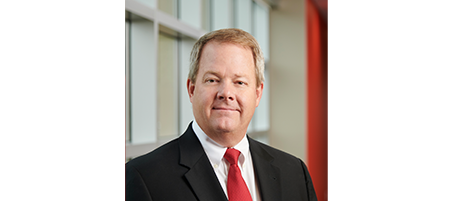
Mark Ruberg is the Packaging Industry Manager for Beckhoff Automation LLC.
Comments